News
Field and CPL Updates
2006 Greenland
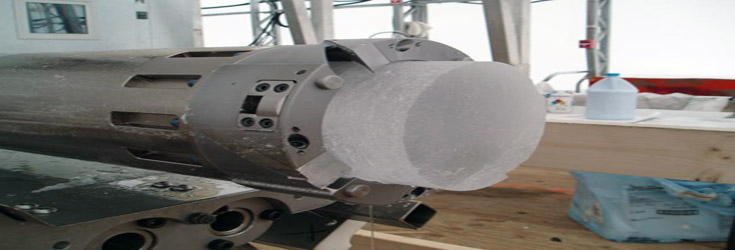
Activity: DISC Drill Test - Summit Greenland
Period: 6/04-6/10/2006
Weather Conditions: Temperature range -28°C to -12°C, wind 1-13 knots.
ICDS Personnel on Site:
Jay Johnson
Kristina Dahnert
Michael Jayred
Bill Mason
Nicolai Mortensen
Paul Sendelbach
Laurent Augustin
John Robinson
Scott Hamon
Other Personnel on Site:
Ed Alexander (Westphal & Company Inc.)
Activities During Period:
Drilling - This week we drilled a total of 161.05 meters. The borehole depth is 282.61 meters. On Wednesday we started working in shifts. We are running two shifts each eleven hours long with one hour off for lunch. The longest continuous core we have drilled was 2.91 meters long. The average core length we can drill before the screen barrels fill, the head plugs, and we lose penetration is 2.6 meters. To reduce the risk of sticking the drill due to the head packing we are typically drilling 2.5 meter cores. Being that we are not using the densifier component of the drilling fluid here in Greenland, the low fluid density may be having an effect on the drill's ability to transport and pack chips into the screen barrels. The sweet spot for the cutter head right now is 100 rpm with a 5mm/second feed rate. We are trying different speed and feed combinations to see if we can drill faster and still maintain quality one piece cores. Once in a while we are getting cores that have a break in them and a chip pack of up to ten centimeters between the pieces. The only theory we have right now is that if the core breaks while drilling the pump is lifting the core and pulling chips into the gap. We have decreased the pump speed from 3000 rpm to 2000 rpm to see if it will lessen the problem. A core barrel was assembled without core sleeves and tested. The core quality was the same as the barrel with sleeves, but the cores were broke into two to four pieces most likely do to the lack of sleeves to support the core on the trip up the bore hole.
Motor section - We have been having an increasing problem with our drill cutter motor not wanting to start. Generally if you jogged it in reverse then started it in forward it would run. Once running it would stay running reliably. The motor eventually didn't want to start at all. We were thinking it was something mechanical until we swapped in our spare motor section and it is acting the same. Right now we can get it to run, but it takes a few tries.
Screen cleaning - We have found that drying the screens between runs aids in chip removal. After the chips have been removed from the screens we are placing them in front of the hot exhaust air from our load bank for about ten minutes. This melts the build up that forms on the inside of the screens. We haven't seen any noticeable gains in pumping efficiency or drilling depth, but the chips come out of the screens easier.
Scoop cutters - We tried out our scoop cutters this week. They took more torque to cut than the flat cutters. The core had deep scores in it, was broke into three pieces, and deep fractures were evident. Not the results we were hoping to see. I am going to inspect the head and cutters to see if something is out of alignment.
Winch - We have found that the winch will only run reliably up to 0.7 meters per second. Running at speeds above that and the level wind drive faults. The night shift has had the level wind fault out consistently at lower speeds where it runs fine on day shift. The only difference between day and night shift is the temperature in the building drops 20o to 40o overnight. I have added heat tape (120 watts) and insulated the level wind motor and gear box to see if it will help. I also added heat tape (120 watts) and insulated the winch drill motor and gear box because the motor was squealing when the temp was 10oF or colder. Paul has added a feature in the software that captures the max tension on the crown sheave while doing a core break. It is working very well.
Instrument section - Nicolai and Paul worked last Sunday and part of Monday to download software updates to the instrument section we installed at the end of last week. They were unable to get all of the files to update so we had to reinstall the original instrument section.
Ed Alexander's last day - Wednesday was Ed's last day at Summit.
Comments (Problems, Concerns, Recommendations, etc.):
Winch control - The level wind drive has faulted five times this week. When this happens you have to bring the drill up using the manual winch control. Moving the lever in the pay in direction the winch control lets the drill free fall for about 50 centimeters before taking control and reeling in cable. This hasn't caused any real problems yet but it needs to be fixed.